toward all directions Shuttle Rack The integration with WMS is the key link to realize warehouse automation management.
First, at the data interaction level, WMS needs to establish a communication interface with the control system of the shuttle shelf. This interface can be realized by wired (such as Ethernet) or wireless (such as Wi Fi, ZigBee, etc.). Through this interface, WMS can transmit inventory information, goods in/out tasks and other data to the shelf control system. For example, when a batch of new goods enters the warehouse, WMS will send the name, quantity, storage location and other information of the goods to the shelf control system, and the control system will command the four-way shuttle to transport the goods to the storage location according to these instructions.
Secondly, in terms of task allocation, WMS assigns reasonable tasks to four-way shuttle shelves according to the overall operation of the warehouse, such as order priority, inventory turnover and other factors. For example, for goods corresponding to emergency orders, WMS will give priority to arranging shuttle buses for outbound operations. In the task allocation process, WMS will consider the current position, running status of the shuttle and the storage layout of the shelves, and optimize task scheduling through intelligent algorithms to improve work efficiency. For example, the route algorithm is used to make the shuttle reach the target cargo location in a way.
Furthermore, in terms of inventory management function, the integrated system can realize real-time inventory monitoring. WMS can obtain the goods status of each location on the shelf at any time, whether it is full, out of stock or partial goods. When the goods move, such as warehousing, outbound or warehouse transfer, the control system of the shuttle shelf will timely feed back the updated inventory information to WMS to ensure the accuracy of the inventory data. At the same time, WMS can also use the integrated system to implement inventory management strategies such as first in, first out (FIFO) or last in, first out (LIFO). For example, in the food or drug warehouse, through the cooperation of WMS and the shelf control system, the goods are delivered in strict accordance with the production date sequence to ensure product quality.
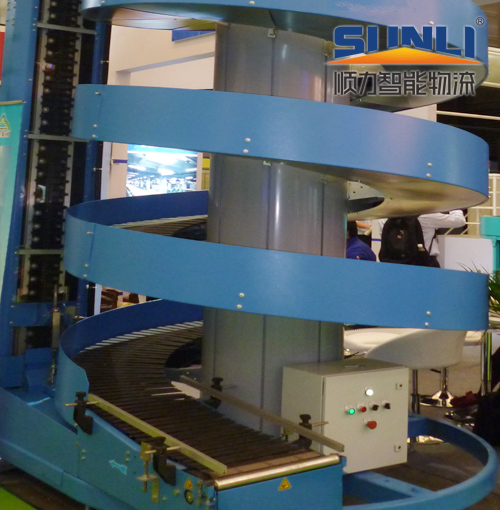
In addition, in terms of visual management of the system, WMS can display the layout of four-way shuttle racks, the running track of shuttle cars, the storage location of goods and other information in a graphical way. Warehouse management personnel can intuitively view the real-time operation of the warehouse through the operating terminal, which is convenient for management decisions. For example, when goods in and out of a certain area are frequently found, management personnel can consider adjusting the shelf layout of the area or increasing the number of shuttle buses.
In order to ensure the stability and reliability of the integrated system, regular system maintenance and data backup are required. Check the communication interface to ensure smooth data transmission; Update the software system to fix possible vulnerabilities and errors; At the same time, backup inventory data and task data to prevent data loss from seriously affecting warehouse operations.