Strategies for balancing storage costs and performance requirements for dense repositories
1、 Reasonably plan the storage system
Shelf selection
Select appropriate shelves according to the characteristics of goods and storage requirements. For example, for goods with high turnover rate and relatively single variety, drive-in rack It is a good choice. It has a high storage density and can effectively use space. Although it may be a little inconvenient for forklifts to access goods inside the shelves, it is cost-effective for specific goods. For goods with multiple varieties, small batches and frequent access, shuttle truck rack system may be more appropriate. Although the initial investment of shuttle truck rack system is higher than that of common rack, its access performance can make up for the cost to a certain extent and improve the overall operation efficiency.
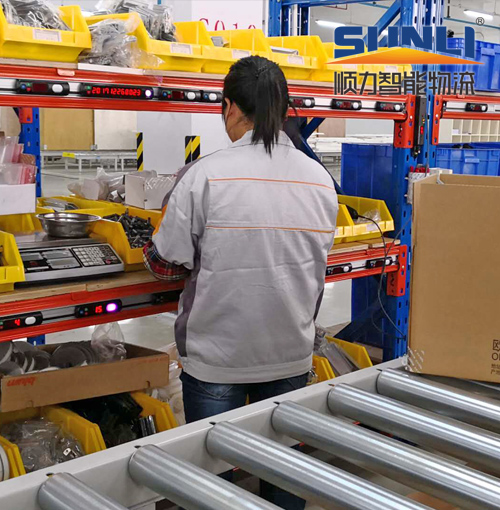
Warehouse layout optimization
Reasonable warehouse layout can reduce space waste. For example, a U-shaped or U-shaped layout is adopted to make the inbound and outbound flow of goods more compact. At the same time, calculate the shelf spacing and channel width, and try to reduce the channel area and increase the storage area on the premise of ensuring the normal operation of the forklift or automation equipment. For example, through logistics simulation software, the turning radius and running track of forklifts are simulated to determine the channel width, so as to reduce the warehouse construction cost without affecting the cargo access performance.
2、 Appropriate application of automation equipment
Automation tradeoffs
Evaluate the need for highly automated storage devices. For large logistics or warehouses with high efficiency requirements, automated intensive storage systems such as automated three-dimensional warehouse (AS/RS) can significantly improve storage performance. It realizes fast storage and retrieval of goods through automatic equipment such as stacker, and reduces manual operation errors. However, the investment cost of this system is huge. Therefore, for warehouses with low storage capacity and turnover rate, semi-automatic solutions can be adopted, such as using shuttles, elevators and other equipment in some areas, combined with manual operation, which can not only control costs, but also improve performance to a certain extent.
Equipment maintenance considerations
When selecting automation equipment, the maintenance cost of the equipment should be considered. Select equipment with reliable quality and easy maintenance, and sign a reasonable maintenance agreement with the equipment supplier. For example, some advanced automation equipment adopts modular design. When a module fails, it can be replaced quickly to reduce maintenance time and cost. At the same time, the equipment shall be regularly maintained to ensure the normal operation of the equipment and avoid performance degradation and additional costs caused by equipment failure.
3、 Inventory management optimization
Increase in inventory turnover
Through effective inventory management methods, such as the strict implementation of the first in, first out (FIFO) principle, to avoid overstock of goods and improve inventory turnover. For dense repositories, a good inventory turnover rate can give full play to its space utilization advantages. For example, inventory management software is used to monitor the stock in/out situation and inventory level of goods in real time, replenish goods and clean up unsalable goods in time, so as to reduce inventory costs while ensuring storage performance.
Reasonable safety stock setting
Reasonably set up safety stock to avoid excessive stock taking up space and funds. Determine an appropriate safety stock level based on historical data and market demand forecast. For example, for seasonal products, the safety stock should be properly increased before the peak season, but it should be strictly controlled in the slack season, so that the storage cost and performance demand can be balanced while ensuring the supply of goods.