In dense repositories, optimizing cargo access processes is critical to improving operational efficiency.
First, the introduction of information management system is a key step. The cargo information is recorded in detail by using the advanced warehouse management system (WMS). Each item has an identification code, such as a bar code or RFID tag. During warehousing, the system can quickly record the basic information of goods, including name, specification, quantity, warehousing time, etc. In this way, when it is necessary to access the goods, the staff can quickly locate the specific location of the goods through the system, reducing the time to find the goods.
Secondly, a reasonable storage layout can help optimize the access process. Classified storage is carried out according to the inbound and outbound frequency of goods. Put the goods frequently in and out of the warehouse in the shelf area near the entrance and exit, which can shorten the handling distance of goods. At the same time, goods of similar specifications or the same batch shall be stored in a centralized manner to facilitate batch access. For example, products of the same type from the same supplier can be stored on adjacent shelves.
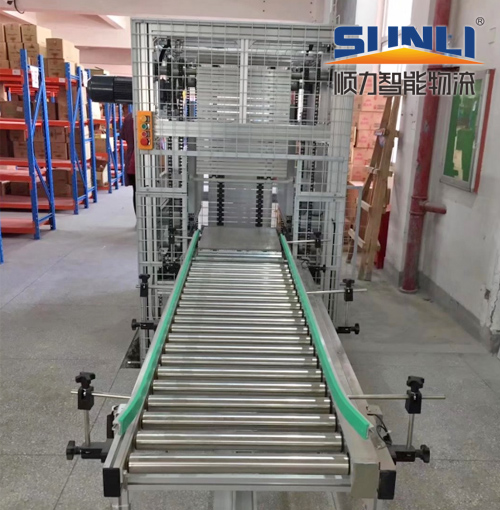
Furthermore, the use of automated devices can improve access efficiency. Equipment such as automatic stacker and shuttle car can run quickly in narrow rack passage. These equipment can take out or store goods from the shelf according to system instructions. Compared with manual operation, automatic equipment is not only faster, but also more accurate. For example, shuttle cars can shuttle between dense shelves to quickly transport goods to locations, reducing the time and physical consumption of manual handling.
In addition, it is also important to establish a picking strategy. For example, batch picking and partition picking are combined. If there are the same goods in multiple orders, you can perform batch picking to pick the goods required by multiple orders at one time. At the same time, the repository is divided into different areas, and each picker is responsible for one area, which can improve the picking efficiency and avoid confusion.
Regularly evaluate and improve the access process. Collect operational data, analyze bottlenecks in the process, such as the storage time of a shelf area is too long or a device often fails, and adjust the storage layout, equipment configuration, or operation process in a timely manner according to the analysis results.