As a highly automated logistics handling equipment, AGV (Automated Guided Vehicle) has a complex software and hardware composition, which is described in detail below:
1、 Hardware components
Body: This is the basic structure of AGV, similar to the body of a car, which is used to carry other parts and provide space for goods. The design of car body needs to consider factors such as bearing capacity and stability. According to different application scenarios, its shape, size and material will be different. There are small and light car bodies for handling light parts, and there are large and solid car bodies that can carry several tons of goods.
Drive system: including motor, wheel, reducer and other components, which is responsible for providing power for AGV to enable it to travel on the predetermined route. Motor is the core of drive, and different types such as DC motor and AC motor can be selected according to needs; The number and layout of wheels can also take many forms, including three wheel and four wheel layouts, to ensure the smooth operation of vehicles.
Navigation system: This is the key part for AGV to realize autonomous navigation. Common navigation methods include electromagnetic navigation, laser navigation, visual navigation, etc. Electromagnetic navigation determines the driving route by laying electromagnetic wires on the ground, and sensors at the bottom of AGV induce electromagnetic signals; Laser navigation uses the laser sensor installed on the vehicle body to scan the surrounding environment, obtain environmental information and compare with the preset map to locate and plan the route; Visual navigation relies on vehicle mounted cameras to collect image information, identify the environment and determine the route through image recognition technology.
Battery and charging system: AGV usually uses rechargeable batteries as its power source, such as lead-acid batteries, lithium batteries, etc. The battery provides continuous power for the operation of AGV, and its capacity determines the operation time of AGV after one charge. The charging system includes charging interface, charger, etc., which can realize the automatic charging function. When the AGV power is insufficient, it can automatically go to the charging station for charging.
On board control system: it is the "brain" of AGV, responsible for coordinating the work of various hardware components, receiving and processing information from navigation systems, sensors, etc., and controlling the driving speed and direction of vehicles according to task requirements.
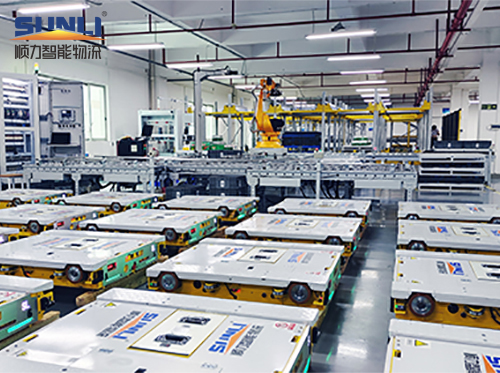
2、 Software components
Navigation software: cooperate with hardware navigation system to realize AGV navigation. The navigation software functions corresponding to different navigation modes are slightly different, but generally, the collected environmental information is processed and analyzed to determine the position of the vehicle in the environment and plan a reasonable driving route.
Task scheduling software: used for task allocation and scheduling management of multiple AGVs. It can reasonably arrange the work tasks of each AGV according to the real-time task requirements of the warehouse or production workshop, such as the priority of cargo handling task, the current position and status of AGV, etc., to ensure the orderly work.
Monitoring software: It can monitor the running status of AGV in real time, including the vehicle's position, speed, battery power, whether it encounters a fault and other information. Through the monitoring software, the operator can timely understand the working condition of AGV at the remote terminal, so as to take measures in time in case of problems.
Human computer interaction software: provides an interface for people to interact with the AGV system, through which operators can issue task instructions to the AGV system, view system related information, etc., to facilitate the management and operation of the AGV system.
The software and hardware components of AGV cooperate with each other to realize its automatic handling function, which plays an important role in modern logistics and production fields.