Compared with traditional vehicles, AGV Security of
Pallet navigation AGVs need to know their location in the manufacturing plant or assembly line in order to navigate effectively. In the relative positioning method, the position is calculated relative to the reference point determined by the factory. With this basic information, we can understand the different navigation methods used by AGV and how to keep safe when working with people.
The magnetic stripe is clearly visible in the factory workshop. AGV can only move along the track filled with tape. People can easily avoid the track and collision with vehicles. These vehicles will also be equipped with proximity sensors. Proximity sensors detect any object in their path by emitting magnetic radiation. There should be no objects in the path of the AGV because it has a dedicated track. These controls are coded so that if anything is detected in their path, the AGV will stop moving.
Use laser technology to obtain 3D maps of their environment. It clearly shows the surrounding obstacles and other objects. This can be used to draw the path. Different from the previous navigation mode, AGV supporting LiDAR does not rely on orbit for navigation. They can cross any path very flexibly. When it detects an object in the path, it can reroute to avoid obstacles.
Fast lasers are used to update the environment model multiple times per second. It helps to detect moving objects, directions and speeds. Complex algorithms can calculate the trajectory of moving objects and draw a path to avoid moving objects.
A sound system can be installed to warn people around them of their methods. It can beep continuously during operation, or beep only when obstacles are detected on the path. A proximity sensor or other existing object detection technology can be used to trigger a warning sound. This will help clear the path.
The truck may be equipped with a common lamp or strobe lamp to indicate its presence. Strobe lights will attract the attention of people around them, and they will definitely avoid them. The lamp can also be used to indicate various states of AGV or manufacturing process. AGV changes its route to accommodate objects in its path. A combination of sensors and computer algorithms can be used to change the path to avoid obstacles.
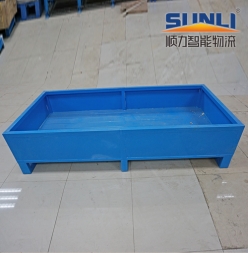