Automatic warehouse is widely used in the field of modern logistics and warehousing. To give full play to its advantages, we need to follow a set of scientific use procedures.
Early planning and familiarity with the system: before starting the automatic warehouse, it is necessary to reasonably plan the warehouse layout according to the factors such as the type of goods, storage capacity, inbound and outbound frequency, etc. At the same time, operators should be familiar with the automatic warehouse management system, including various operation interfaces, instruction input methods, data query functions, etc. Only by mastering the system, can the follow-up work be carried out smoothly.
Goods Receipt Process: After goods are delivered to the warehouse, information is entered first. The name, specification, quantity, batch and other information of the goods can be accurately entered into the system by scanning the code or manually entering. Then, the system will automatically allocate storage locations according to the preset storage strategy. The goods are transported to the storage location through the conveying equipment, and the goods are stored on the shelf by the automatic equipment such as the stacker. In this process, it is necessary to ensure that the goods are well packaged and clearly marked, so that the system can accurately identify and manage them.
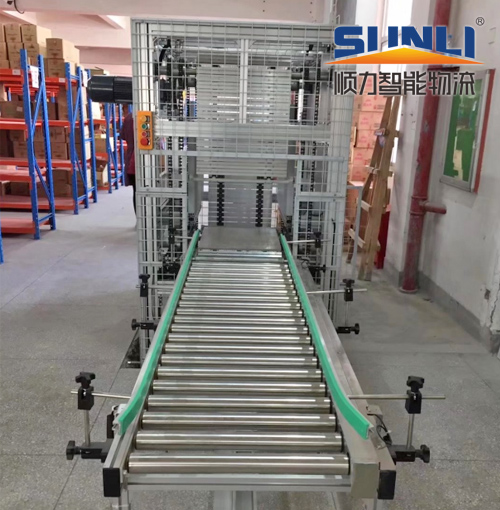
Storage management: The storage management of automatic warehouse relies on advanced software system. The system monitors the storage status of goods in real time, including inventory quantity, location occupancy, etc. Inventory can be counted according to the actual demand, and the system generates a count report to quickly check inventory variance. In addition, it can also manage the goods by category. For example, it can reasonably adjust the storage location according to the factors such as shelf life and value, so as to facilitate the priority delivery management.
Goods issue operation: when there is an issue demand, enter the issue instruction in the management system to specify the required goods information. The system quickly retrieves the location of the corresponding goods according to the established rules, and issues the issue task. The automation equipment takes the goods out of the storage location and transports them to the delivery area through the conveyor line. The operator checks the cargo information again and completes the shipment after ensuring that there is no error. In the whole process of ex warehouse, attention should be paid to close cooperation with upstream and downstream links, such as transport vehicle scheduling, to ensure that goods are delivered to the destination in a timely and accurate manner.
By strictly following these steps, from early planning to daily warehousing, storage, and outbound operations, automated warehouses can operate stably, playing a key role in improving the efficiency of warehousing management and reducing operating costs for enterprises.