Shuttle Rack As an automated warehousing solution, the system can significantly improve storage density and access efficiency. However, in order to ensure its long-term stable operation, system maintenance and troubleshooting are very important. The following are some key points for the maintenance and troubleshooting of shuttle racks:
1. Regular inspection and maintenance
The core part of the shuttle rack system is the shuttle car, the rack and the control system. In order to ensure the operation of the system, regular inspection and maintenance are required:
Shuttle inspection: the shuttle is the main working unit of the shuttle rack system, and it needs to regularly inspect the key components such as wheels, batteries, motors, and transmission systems. Regularly clean the driving device of the shuttle, check the charging state of the battery, and ensure that the battery is sufficient.
Shelf inspection: regularly check the stability and bearing capacity of the shelf to ensure that there is no damage at all levels of the shelf. In particular, check the guide rail system of the shelf to ensure that the guide rail is not deformed, loose or dusty, so as to avoid affecting the smooth operation of the shuttle car.
Electrical system inspection: regularly check the circuit, sensor, control panel, etc. of the electric control system to avoid electrical failure affecting the system operation. Check and clean the sensor to ensure its normal operation.
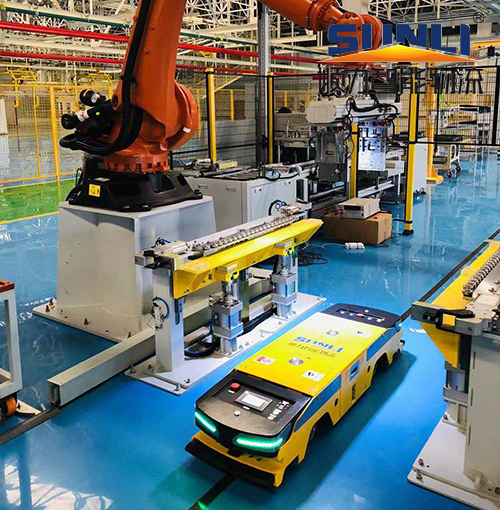
2. Cleaning and lubrication
Keeping the system clean and lubricated is one of the key factors to ensure its operation:
Shuttle lubrication: lubricate the moving parts of the shuttle regularly, especially the wheels and bearings. Proper lubrication can reduce friction, improve movement efficiency and prolong equipment life.
Track and shelf cleaning: If there is dust or water on the track, it may affect the running speed and stability of the shuttle car, so the track needs to be cleaned regularly. The shelf surface shall be kept clean to prevent dust and garbage from affecting the access of goods.
3. Battery and electrical equipment maintenance
Shuttle buses are mostly electrically driven, and the battery is the key energy source. Battery maintenance is critical:
Battery inspection and replacement: regularly check the battery power, charging state and battery life. The aging or damaged battery shall be replaced in time to avoid affecting the running time and stability of the shuttle.
Electrical system inspection: regularly check the electrical control system to ensure that there is no short circuit, poor contact and other problems. At the same time, check whether the control panel and PLC controller operate normally to ensure the accuracy and response speed of the system.
4. Software and system upgrade
Shuttle rack system relies on advanced control system and software to realize automatic operation. Therefore, it is very important to keep the software updated and system optimized:
System upgrade and debugging: regularly upgrade the software of the control system to repair possible vulnerabilities or improve system functions. In addition, with the change of warehouse operation requirements, the system debugging also needs to be optimized according to the actual needs.
Data backup and recovery: regularly back up the data of the control system to prevent data loss caused by hardware failure. Ensure that data can be recovered in time in case of system failure to ensure the continuity of operation.
5. Troubleshooting
When the shuttle rack system fails, timely and effective troubleshooting can reduce downtime. Common faults and solutions include:
Shuttle does not run: if the shuttle cannot be started, first check whether the battery is sufficient and whether the electrical system is connected normally. Secondly, check the motor and drive system of the shuttle to ensure that there is no clamping stagnation.
Goods cannot be stored and stored normally on the shelf: if some items in the shelf cannot be stored and stored successfully, first check whether the guide rail is clean and not blocked, and check whether the sensor works normally.
System communication failure: the communication failure between the shuttle car and the control system will cause the system to fail to operate normally. At this time, it is necessary to check whether the wireless network or wired network connection is normal, and ensure that there is no signal interference between the sensor and the control device.
Slow system response or failure: if the system response is slow, it may be due to aging of electrical components or control program error. It is necessary to check the hardware equipment of the control system, and restart or restart the program if necessary.
6. Operator training
Ensuring that operators are familiar with the operation and maintenance process of the system is also an important aspect of preventing failures and improving system efficiency. Operators shall participate in training regularly to understand the working principle, routine maintenance and emergency handling procedures of the shuttle rack system.
conclusion
The maintenance and troubleshooting of the shuttle shelf system requires careful work. Regular inspection, cleaning, lubrication and maintenance of batteries and electrical equipment are key to ensure long-term stable operation of the system. Through timely troubleshooting and timely system upgrading, the working efficiency and service life of the system can be improved.