In the planning of the new factory, the traditional shelf+manual warehouse system is still used for the equipment in the warehouse Automatic stereo library The system of Stereoscopic library Only dozens of operators in the warehouse were killed, or only some space was released, saving some land area. It is difficult to calculate the corresponding remuneration period from the contribution remuneration period of the financial algorithm. From the perspective of logistics operation, this paper points out several direct advantages of the automated warehouse system.
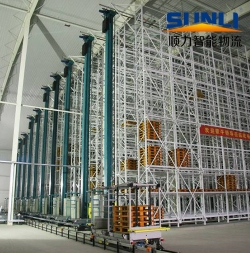
1、 Inventory processing
Through WMS information system processing and full mechanical operation, it can ensure severe first in first out, real-time visual inventory data, and prevent expired inventory. According to the general inventory difference of 3%~5% in the traditional warehouse, this part of differential inventory can be converted into cash flow from the financial point of view by using the automated stereoscopic warehouse system. From the warehouse point of view, logistics personnel do not have to spend 1 to 2 days every month to check inventory to find this kind of difference inventory.
The warehouse can also define a safety stock for various materials. When the safety stock is reached, the system can actively alert for replenishment, and then reduce the risk of lack of inventory supply.
2、 Accurate distribution
For production logistics enterprises, accurate distribution refers to delivering the exact number of materials to the exact address on time. One of the three criteria is indispensable. The traditional approach is to invest a lot of warehousing manpower to carry out sub packaging, sorting and integration. Due to the participation of manpower, it is difficult to completely ensure the complete accuracy of distribution even under the perfect distribution process. The output of the assembly line complies with the barrel benefit. If the materials of one station are affected, the output of the whole line will be affected. However, automated logistics greatly reduces the risk of waiting for materials due to manual distribution.
3、 Safe and efficient
The existing enterprises mainly transfer forklift, hydraulic transfer truck, tractor, etc. Forklifts are only suitable for use in assembly storage areas with fewer people. When transferring to the production area full of people, it is necessary to use other relatively safe transfer things, and the center must increase the transfer breakpoint. Many enterprises use forklifts to deliver materials directly, and forklift incidents also emerge in endlessly. With the ASRS system, the transfer equipment can be directly connected to the storage system, which is more secure and efficient.
4、 Quality control
In manufacturing enterprises, many quality problems are not the problems of poor incoming materials and production process, but the materials are not stored as required after receiving or are subjected to rough manual operation during the transfer process. Automatic transportation can prevent this kind of problem and improve the production and quality.
5、 Corporate image
Many enterprises still focus on production rather than logistics. For example, the production workshop has now used the internationally advanced production equipment, but the material transfer is still the original shoulder to shoulder, which is not in line with the enterprise's image. On the basis of saving area and reducing labor, the self initiated logistics equipment can also greatly promote the image of the enterprise itself and show its sharp edge in the fierce operation competition.