Product Introduction
The single extension column stacker is the core equipment of the automated warehouse, which requires not only accurate and fast positioning, stability and reliability, but also safety and security during work.
The stacker consists of upper and lower crossbeams, columns, cargo platforms, counterweights and various telegraph control elements. The stacker relies on the host machine to walk, the cargo platform to rise and fall, and the fork expansion and contraction to make the unit cargo move in three directions of the warehouse, thus realizing the task of putting the cargo into/out of the shelf. The working capacity of the stacker determines the Z capacity of the entire automated three-dimensional warehouse. Stacker is the core equipment of the entire automated warehouse Through manual operation, semi-automatic operation or fully automatic operation, the goods can be transported from one place to another.
The stacker system made of linear motor has the following characteristics:
1. High speed stacking, free position setting
2. Higher output, uninterrupted continuous stacking
3. Improve product quality, avoid material surface contamination and damage caused by manual stacking, and ensure the quality of material surface
4. Quickly change the product series to control the force
5. Improve efficiency
Simple structure
The traveling motor drives the wheel horizontally on the lower guide rail through the drive shaft, the lifting motor drives the cargo platform for vertical lifting movement through the lifting wire rope, and the fork on the cargo platform for telescopic movement.
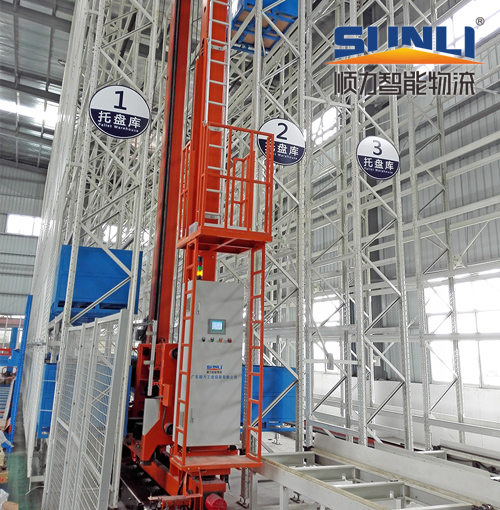
working principle
The goods in the designated location can be taken out or sent to the designated location through three-dimensional movement. The horizontal bar code addresser is used to control the horizontal travel position of the stacker, the vertical bar code addresser is used to control the lifting position of the pallet, and the proximity switch is used to control the telescopic position of the fork. Realize computer control through conversion of optical communication signal
Full automatic control
Manual and semi-automatic control of on-board control cabinet can be adopted.
Product performance
S/N | Project | Description |
one | Main material | Q235, Aluminum profile |
two | Number of handling units | Generally, one unit is transported at a time or made as required |
three | Handling unit size | Standard tray 1200 * 800mm, 1200 * 1000mm or as required |
four | Unit cargo weight | 10~2000kg or as required |
five | running speed | 5 ~ 240m/min, variable frequency speed regulation |
six | Lifting speed | 5~50m/min, variable frequency speed regulation |
seven | Fork speed | 40m/min |
eight | Fork brand | Mias or equivalent brand or self production |
nine | positioning accuracy | ±5mm |
ten | Positioning mode | Laser address recognition or barcode positioning |
eleven | control mode | Manual, semi-automatic, online full automatic |
twelve | supply voltage | Domestic standard power frequency industrial power, 3-phase, 380V, 50Hz |
thirteen | Power supply mode | trolley |
fourteen | Communication mode | wired |